-
Welcome to 205GTIDrivers.com!
Hello dear visitor! Feel free to browse but we invite you to register completely free of charge in order to enjoy the full functionality of the website.
-
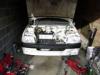
[trackday_prep] Project 150
By
RossD, in Trackday & Race/Rally Prep