-
Welcome to 205GTIDrivers.com!
Hello dear visitor! Feel free to browse but we invite you to register completely free of charge in order to enjoy the full functionality of the website.
-
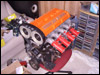
[project] Project 205 Xu13j4
By
B1ack_Mi16, in Large Scale & Special Projects