-
Welcome to 205GTIDrivers.com!
Hello dear visitor! Feel free to browse but we invite you to register completely free of charge in order to enjoy the full functionality of the website.
-
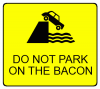
[Project] 205 Dimma S16 Turbo Converting To 4X4
By
lybker, in Large Scale & Special Projects