-
Welcome to 205GTIDrivers.com!
Hello dear visitor! Feel free to browse but we invite you to register completely free of charge in order to enjoy the full functionality of the website.
-
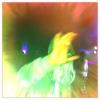
Removing Rear Stub Axle To Free Ceased Bearing.
By
kyepan, in Brakes, Suspension & Steering