-
Welcome to 205GTIDrivers.com!
Hello dear visitor! Feel free to browse but we invite you to register completely free of charge in order to enjoy the full functionality of the website.
-
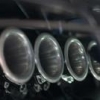
Be Box Rebuild/refresh/refurb Part Sourcing, And Be1-3 Part Crossover
By
welshpug, in Gearbox & Drivetrain