-
Welcome to 205GTIDrivers.com!
Hello dear visitor! Feel free to browse but we invite you to register completely free of charge in order to enjoy the full functionality of the website.
-
Sign in to follow this
Followers
0
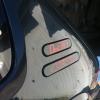
Gotta Drill Out A Wheel Bolt
By
pugpete1108, in Brakes, Suspension & Steering