-
Welcome to 205GTIDrivers.com!
Hello dear visitor! Feel free to browse but we invite you to register completely free of charge in order to enjoy the full functionality of the website.
-
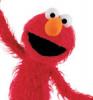
[engine_work] 1.9 8v Engine & Front End Refresh
By
Bogsye, in Engine Work