-
Welcome to 205GTIDrivers.com!
Hello dear visitor! Feel free to browse but we invite you to register completely free of charge in order to enjoy the full functionality of the website.
-
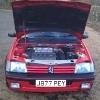
[car_upgrade] 205 Gets An Extra 2 Cylinders
By
thirdtimelucky, in Car Restorations, Overhauls & Upgrades