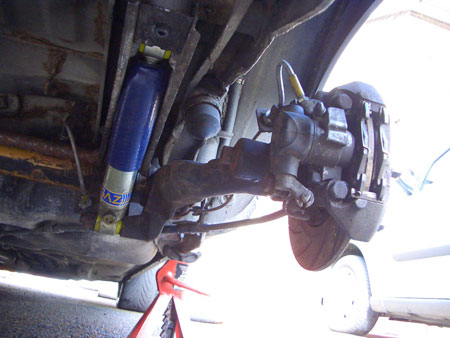
If you are going to attempt this:
Print these Instructions and read them carefully. Allocate an hour to examine the rear axle and make sure you can identify all the components talked about in these instructions and that you have all the relevant tools. These instructions are intended as an accurate guide. If you are not 100% certain of what you are doing consult a specialist.
1. Jack the car up at the back and remove both wheels.
2. Remove the spare wheel, and spare wheel cage. (For easier access to the axle)
3. Unbolt the rear shocks from the rear radius arms and swing them up towards the boot floor of the car. In unbolting the shock you will release the bracket that carries the flexible brake line.
The Next steps should be performed on one side of the car then repeat for the other side:
4. On the radius arm there is a bracket that carries the hand brake cable and the solid brake line, release the handbrake cable and brake line from the bracket. Remove the 13mm bolt that secures the bracket to the radius arm. If you look at the Radius arm there is a plate that is secured by the same bolt that secures the bracket that carries the handbrake cable and solid brake line. The plate is pressed into the radius arm and in the center is a dust cap (approx 15mm in diameter) this can be unscrewed using a type 40 Torx tool.
5. Into the hole that you have just removed the Torx dust cap from gently wind in a well greased 19mm head bolt. The bolt needs to be at least 100mm long.
6. As you wind the bolt in (Expect resistance) the plate will start to come away from the radius arm. Keep winding the bolt in until the plate comes completely off of the radius arm. Remove the 19mm head bolt from the plate.
7. Look under the car and you will see the two torsion bars. One in front of the axle and the other behind. The relevant torsion bar is inserted into the radius arm you are working on. Now proceed round to the other side of the car, trace the torsion bar for the radius arm you are working and you will see that it inserts into a fixed casting on the axle. Sticking out the other side of the casting you will see a threaded stud with a screwdriver slot in it and a 13mm locking nut at its base. This is screwed into the torsion bar. Spray the locking nut and threaded stud with a lubricant (WD40) and undo the 13mm locking nut (Carefully). Then unscrew the threaded stud using a suitable screwdriver until considerable resistance is felt (The stud may be fairly hard to undo take care not to round out the slot cut in the end).
8. As soon as the threaded stud is undone the radius arm is free to be moved off of the end of the axle enough to allow adjustment of the torsion bar. However it is important to mark the torsion bar where it enters the casting. The end of the torsion bar is splined and so is the inside diameter of the casting. If you get a heavy mallet and knock the back edge of the radius arm driving it away from the center of the car (Slowly). You will see the splines on the end of the torsion bar start to appear out of the casting. At this point stop and mark one of the splines on the torsion bar and where that spline enters the casting. This will give you a reference point of your original ride height setting. When you are confident that your marking of the torsion bar is accurate continue driving the radius arm off of the axle until the torsion bar comes completely out of the casting. When you reach this point the radius arm will not fall off of the end of the axle but will swing down.
9. For this part you will need an assistant. Get your assistant to take hold of the radius arm while you take hold of the torsion bar. The assistant should lift the radius arm up into the wheel arch supporting it with their hands. Then you will using your original markings on the torsion bar and casting instruct your assistant to rotate the radius arm up into the wheel arch until you have advanced the radius arm up by one spline. Get your assistant to slowly slide the radius arm back into the axle, meanwhile you guide the torsion bar back into the casting. Just before your assistant pushes the radius arm home you should still be able to see the splines and your markings check that you have only rotated the radius arm up by one spline. When happy push the radius arm home as far is it will go. Now screw the threaded stud back in as far as it will comfortably go, drive the radius arm fully home using a mallet if necessary. Then wind the 13mm locking nut back down the threaded stud nice and tight.
10. The plate that presses into the radius arm should now be re-inserted. Before you insert it make sure it is in the approximate position that it was when you removed it, the hole in the end of it that the 13mm securing bolt goes through should line up with the threaded hole in the radius arm. To re-insert it will require a fair bit of effort you will need to use a mallet, be gentle though until you are sure that the plate is properly located and lined up and is travelling into the radius arm correctly and not at an angle. Drive the plate fully home, the 13mm bolt that secures the plate and the bracket that carries the handbrake cable and solid brake line should easily screw into its hole in the radius arm. If not remove the plate again (Follow steps 5 & 6) rotate the plate and re-insert it so the hole for the 13mm bolt lines up with the threaded hole in the radius arm. As soon as you are confident that the 13mm bolt will screw into the radius arm okay put the bracket that carries the handbrake cable and solid brake line back in place and screw the 13mm bolt fully home and tighten. Re-attach the handbrake cable and solid brake line.
11. Screw the torx dust cap back into the plate and tighten (Don't Over tighten)
12. Finally pull the rear shock back down and bolt it back on to the radius arm remembering to put the bracket that carries the flexible brake line back in place. You will need an assistant to push the radius arm down a bit to get the bottom of the shock to line up with its bolt because remember you have rotated the radius arm up into the arch. Tighten the shock securing bolt to the specified torque setting (See Haynes manual).
13. Now repeat step 4 to 12 for the other side of the car.
14. Replace the spare wheel cage and spare wheel. Replace the wheels. Let the car back down onto the ground.
15. You must now inspect the bump stops (Cone shaped rubber blocks bolted to the car to stop the radius arm bottoming out). If these are in contact with or very close to the radius arm then they will need cutting down to allow some suspension travel.
You have now successfully lowered the back of your Peugeot 205. The drop will vary from car to car depending on the amount of flex in the torsion bars. But on average you should see a lowering effect of around 40-50mm.